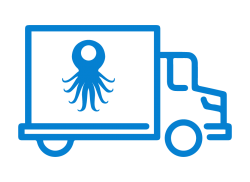
Implementation
Ensuring the virtual world matches the real world
OCTOPUZ offers implementation services to ensure the virtual world created within OCTOPUZ exactly matches your real-world physical robot system(s).
What to Expect?
Implementation is the process of calibrating real system components with those in the virtual world. A digital twin is created, allowing users to program their robotic applications using Offline Robot Programming (OLRP). The overall process involves identifying all components in the cell, analyzing their behaviour, configuring the robot controller settings, calibrating the virtual component locations, and verifying the system. Afterward, robot-specific code is then generated to be run on the real system.
How Does it Work?
OCTOPUZ's SMART Implementation process equips users with the necessary skills and reinforces the concepts needed to implement successfully. A digital twin is created, allowing users to program their robotic applications using Offline Robotic Programming (OLRP) and then generate robot-specific code run on the real system. This process consists of five unique steps: Survey, Measure, Align, Repeat, and Test. The SMART process ensures that all components and alignments are properly calibrated and tested before the end of the service.
Survey
The first step is to identify all components in the real system that will need to be calibrated to have an accurate representation of the cell in OCTOPUZ. This includes robots, externals, stationary objects, and any other components necessary based on the cell setup.
Measure
This process involves taking a wide range of points using the real robot to locate all components in the cell relative to the robot itself. We collect as many points as needed to ensure all inaccuracies and errors are dialed in to ensure overall accuracy.
Align
Once measurements and kinematics are verified, the point data recorded is imported directly into the OCTOPUZ software. This begins the iterative process of aligning components. Each alignment is followed by a verification program that is loaded on the real system and touched up.
Repeat
The process of survey, measure, and align is continued for all components until each component identified is located accurately within the OCTOPUZ cell.
Test
Our team ensures the system is running as expected using OCTOPUZ generated code before the service is complete.
Why Does it Work?
Our implementation service is something that we take pride in. Whether it is something complex or simple, we take the time to walk customers through their solutions. We are dedicated to the customer throughout the entire process to ensure all steps are completed successfully and performed accurately.
OCTOPUZ Implementation Options
On-Site Implementation
When an on-site implementation is possible, an OCTOPUZ Applications Engineer travels to your facility. When on-site, we begin by importing your CAD file(s), robot, and external axes into OCTOPUZ. We then run calibration programs to test and confirm the accuracy of the virtual cell. Once your OCTOPUZ setup is complete and verified, our Applications Engineer conducts on-site training at your facility, so you can confidently navigate the software.
Remote Implementation
Our OCTOPUZ Remote Implementation (ORI) service enables you to calibrate your physical robot systems with the OCTOPUZ software. During your ORI, you have a dedicated OCTOPUZ Application Engineer who will guide you through every step of the calibration process, assist you with any challenges that arise, and ensure your calibration is successful.
Our ORI service is a great option if any of the below is true:
- Travel to your site is restricted or limited.
- Production downtime is limited (minimal access to the robot).
- Your organization has a strong background in robotics (or the system being calibrated).
- There are multiple systems to be calibrated, or there are future plans to make adjustments or add components to the physical system.
OCTOPUZ in Real Life
KUKA Weld Cell On-Site Implementation
York Metal Products is an OCTOPUZ customer using our offline robot programming software to easily program their KUKA Weld Cell offline on a computer to realize benefits like decreased programming time and decreased robot downtime. This is a great system designed and set up by Penmar Automation Inc.
Cell details:
- Integrator: Penmar Automation
- Robot arm: KUKA KR 20 R3100
- Controller: KRC4
- Externals: Indexing rotary with two 2-axis tilt-rotate positioners (S1 and S2)
- Options: Touch sensing, weaving
- Application: Arc welding
- Programming: OCTOPUZ Offline Programming
KUKA Robotic Polishing Implementation
Mancor has been a great long-term customer using OCTOPUZ OLRP software to program multiple robotic weld cells across multiple facilities in North America. The video you see below is a recent implementation of a new polishing application. Love seeing this in action for production.
Cell details:
-
-
- Robot arm: KUKA KR 210 R2700
- EOAT: PushCorp - STC0612BT40 with an AFD1240 Active compliance device.
- Externals: 1-axis rotary positioner
- Application: Robotic polishing
- Programming: OCTOPUZ Offline Programming
-
Fanuc 10 Axis Weld Cell On-Site Implementation
Our Applications Engineering team completed an onsite implementation of OCTOPUZ OLRP software for a Fanuc weld cell at Ateliers BG in Quebec, Canada. After the implementation, this 10 axis cell is now accurately calibrated in OCTOPUZ and ready to be easily programmed offline for increased efficiencies! Production ready!
Cell details:
-
-
- Robot arm: Fanuc M-20iA/12L
- Externals: 2 axis linear track and 2 HS/TS positioners
- Application: Arc welding
- Options used: Laser searching, weave, stitch, multi-layer
- Programming: OCTOPUZ Offline Programming
-
KUKA Weld Cell On-Site Implementation
The Applications Engineering team at OCTOPUZ recently conducted an onsite implementation of OCTOPUZ Offline Robot Programming Software at the ESAB Robot Lab in Gothenburg Sweden. This KUKA weld cell is being used to support customer demos, applications development, and R&D activities. The cell is currently being used on a project with a major steel producer to characterize the Hybrid Laser weldability of a new high-strength steel for lightweight applications.
Cell details:
-
-
- Robot arm: KUKA KR 90 R2900 extra HA
- Linear track axis: KUKA KL4000
- 2 axis rotary positioner: KUKA DKP-400
- Application: Laser hybrid welding
- Programming: OCTOPUZ Offline Programming
-
Fanuc Weld Cell Remote Implementation
The Applications Engineering team at OCTOPUZ conducted a remote implementation for a new customer recently. The cell had a very common configuration we have seen with a Fanuc M-20iA/12L robot and a headstock-tailstock positioner for both indexing and coordinated motion, depending on the weld seam. The customer will be touch sensing the entire tank part first to locate the seams which allows them to minimize the additional cycle time that accompanies torch clean routines. All welds are using weave parameters and seam tracking. We successfully programmed another high mix/low volume production customer utilizing OCTOPUZ.
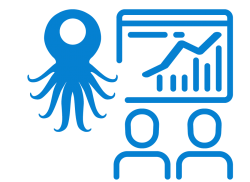
Training
Become a robot programming expert
As part of our commitment to our customers, we offer full training to ensure you are comfortable using OCTOPUZ to program complex robot applications. Training can be in person at your facility or by remotely via video tutorial.
Request Training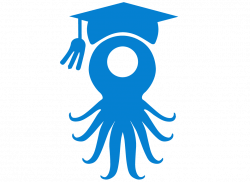
SOFTWARE PLAN BENEFITS
Stay on the cutting edge of Offline Robot Programming
The benefits of an active OCTOPUZ software plan (active subscription or active maintenance for perpetual licenses) include access to OCTOPUZ software updates, dedicated technical support services, online learning resources, and more.
OCTOPUZ Software Updates
The robotics industry is fast paced. As such, the OCTOPUZ team is dedicated to continuously improving OCTOPUZ with regular updates that add new enhancements and product features.
When a new update for OCTOPUZ is released, you are immediately notified. You then have control of when you apply new updates, ensuring your users are always as productive as possible.
Dedicated Technical Support Services
For any question, challenge, or issue you encounter in OCTOPUZ, our world-class, dedicated Support Team is here for you. We make it easy to submit a support request through the OCTOPUZ Community and Support Center ticket submission system, or through email.
Our team of technical support specialists are on-hand to promptly address all of your concerns. The success of our users is our top priority!
OCTOPUZ Academy
The OCTOPUZ Academy is your complete guide to learning the OCTOPUZ software. Always up-to-date, it makes learning how to program robots offline in OCTOPUZ simple.
- DOCS AND GUIDES: step-by-step tutorials on how to program in OCTOPUZ and how to use features and complete workflows.
- VIDEOS: voice-guided video tutorials complete with follow-along downloadable cells, from the basics to more advanced concepts for a variety of application-specific tasks.
- OTHER RESOURCES: guided documentation on implementation and other important robot-specific information.